High Pressure Laminate… it’s made of paper!
High Pressure Laminate… it’s made of paper!
Have you heard the myth that laminate is made of plastic? It’s not true! The primary material used to create our decorative laminate sheets is naturally occurring sustainably sourced paper.
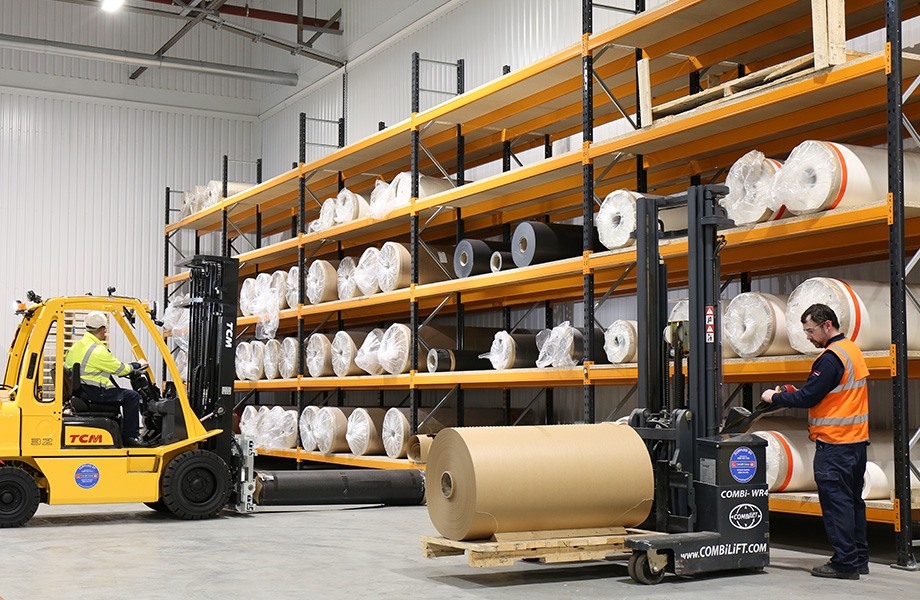
How do you make HPL?
To make our renowned Formica® Laminate, kraft paper, which forms the core of the material is impregnated with resin and pressed together at high pressure and temperature with a resin impregnated “decor” paper. The high pressure laminate (HPL) process not only gives the laminate sheet it the colour and surface aesthetic but gives it a high resistance to wear, impact, heat and staining.
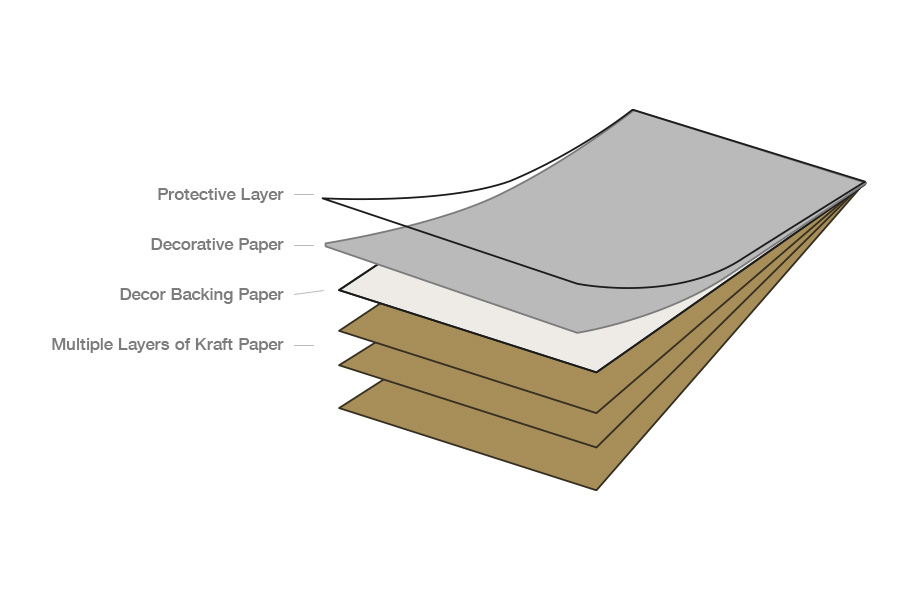
This process makes the completely sealed, hardwearing and hygienic surface we all recognise.
A quick and easy guide to the laminate sheet production process
Whether you are using Formica Laminate sheets for internal doors, washroom cubicles, a kitchen or for bigger projects such as hospitals, schools, hotels, offices or restaurants, the manufacturing process remains the same.
Stage one: paper impregnation
First, the kraft paper which makes up the finished product’s base is fed on a roll through a machine that impregnates it with phenolic resin. This gives the laminate sheet the strength and rigidity it needs. Once dried, it’s stored ready for use later in the production process.
Meanwhile, the surface paper and top paper are impregnated with melamine resin to generate the laminate’s decorative finish and durability.
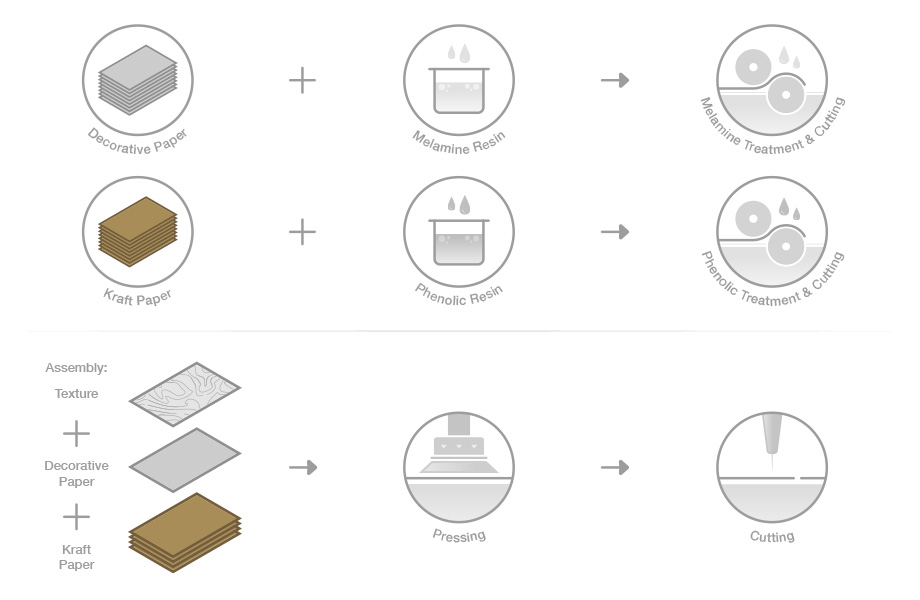
Stage two: pressing the laminate sheets
Using a large press, the treated paper sheets are assembled into packs and layered between steel plates. Then they’re heated to 150°C and compressed under a pressure of 0.5-0.75 tons per square inch for just over an hour. Once they’re removed and cooled, they’re cut to size and checked for quality control.
Learn more about our wide range of products for commercial interiors and order your free samples online today.